|
|
Tuesday, August 21st, 2018
I've been fretting about carving the pegbox on my cello... Today I had an idea for how to hugely simplify the process. I can't swear it is a good idea, but I went ahead and acted on it. Won't know until setup time if it's a boon or a bust.
The lateral* pegbox
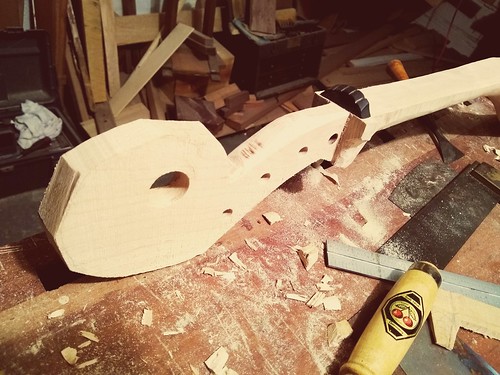
So the idea is, instead of having two ⅜" cheeks for the peg to enter and exit, with the string winding in the middle, there is just a central fin ¾" wide. Pegs enter from alternating sides; the string winds on the opposite side to where the peg enters.
 The good
It looks kind of cool; it's original; it's way simpler to make. Also: if I ever wanted to switch to 5 strings, easy to drill another peghole.
The bad
I'm not certain about the physics here. In a traditional pegbox, the stress on the string is in between two points of support; here, the stress will be supported on one side only. This may break the peg, I'm not sure how strong they are. We'll see! If I'm wrong and it does not work, I'll need to carve a new pegbox and scroll, and graft it onto the neck. (Or as Jeff points out, if the pegs don't work I could try using bass viol tuning machines as a fallback option.)
but
Here's why I'm sort of confident about the peg holding up: if the string is wound properly, the stress on the peg will be right next to where it emerges from the supporting wood. This seems like a pretty strong load-bearing point.
*(and note)
Not a huge amount of thought went into the nomenclature. If you've got a more descriptive adjective for this than "lateral", please let me know.
↻...done
posted evening of August 21st, 2018: 2 responses ➳ More posts about The Tin-can Cello
|  |
Sunday, August 12th, 2018
Work plan for building the Tin-can cello (this post is changing a bit, I'm just going to edit it inline; further edits in comments):
- Flatten bottom of neck: this will be the reference flat when cutting on the bandsaw. Plane entire length of board flat and straight. For reference, this is going to be parallel to the plane of the washtub's base. [note I never planed it flat, at all.]
- Mark up neck: draw outlines of the dowel and the neck on the board. Draw outline on the top of the board (i.e. opposite the side that was planed in step 1) and on one side. Use cardboard cut into shape of tub profile to determine where the dowel will go into the bucket.
- Cut around the outlines on bandsaw.
- Rough out dowel and neck. Finish dowel so it is straight and true. Mark up pegbox and scroll. Drill pilot holes for pegs.
- Mark entry for dowel on bucket. Cut open using angle grinder. Mark exit hole for dowel. Cut open.
- Fit dowel into bucket. True up heel.
- Finish shaping neck, carve pegbox and scroll. Attach nut and fingerboard to neck.
- Mount tailpiece; put A and C strings on, loose.
- Mark up and carve bridge.
- Set up cello.
posted evening of August 12th, 2018: 3 responses ➳ More posts about Projects
|  |
(Roughly to scale anyways). Some key measurements, as follows:
- Scale length (bridge to nut) 27.4"
- diameter of soundboard 17"
- bridge position to edge of soundboard ~4"
- length of peg box + scroll ~9"
- length of fingerboard 23 ⅜"
- height of tub 11"
- width of fingerboard at bridge end 2 ⅜"
I reckon the blank for the neck will need to be 10/4 hard maple, 6" wide*, 5' long. (Hope my bandsaw is up to the task! Derek is coming over in the near future to help with tuning it, and also to help with picking out wood...)
posted afternoon of August 12th, 2018: 7 responses ➳ More posts about Luthery
|  |
Two excellent resources for carving and setting up the bridge -- Fitting and Carving a New Cello Bridge at Triangle Strings lays it all out, Cello Bridge Carving at Jawmunji Fingerstyle Resources breaks down and simplifies a few
key points.
I bought a good quality Belgian-style bridge from Menzel and a template from Metropolitan. Won't do much work on it until the main work of building the instrument is done... I'm already starting to visualize where its contours will be.
.
posted morning of August 12th, 2018: Respond
|  |
Wednesday, August 8th, 2018
So here is the idea: to build a cello, using as resonating chamber a washtub + a bass drum head. The construction of it will be on the principle of a gourd banjo; but with curved nut, fingerboard, and bridge. I am using an 11-gallon steel washtub, 20" across at its widest point; splurged and ordered it from Amazon -- consider this circular form the lower part of a cello body. The position of the bridge will be near the top of the soundboard, meaning the neck will need to be a bit longer than the the fingerboard* -- unlike a cello, which has a longer body. So the spot where you're bowing is at the top of the circular soundboard (the soundboard, i.e., the bottom of the washtub), midway between the end of the fingerboard and the bridge. The drum head is clamped in to the back of the body, to enclose the resonating chamber; and I'll cut a soundhole in the side of the tub. The instrument is in effect a bowed banjo-cello, with no soundpost -- a baritone rebab. I've got my fingers crossed that it will sound like anything :). I find it encouraging that a few experimental taps at the soundboard made the bucket ring like a bell!
First step is of course to have the washtub and cello components in hand, so I can mark it all out on cardboard. Local violin dealer Mo Menzel has very graciously offered to sell me a broken cello cheap, to use for parts, and I'm hoping she'll sell me a good bridge as well. In the next week or so, will swing by Board and Beam in Fairfield to pick up a hard maple board for the neck.
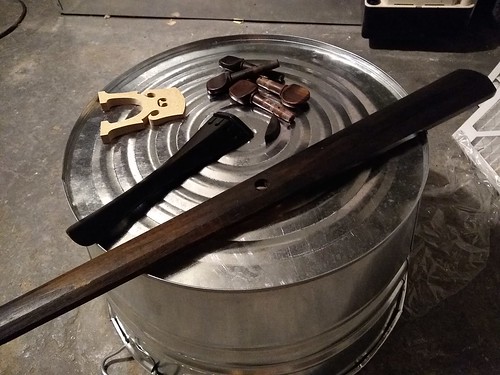
posted evening of August 8th, 2018: 1 response
|  |
Sunday, June 17th, 2018
I spent the past week in Long Branch at a instrument-making workshop taught by Jeff Menzies of Menzies Instruments, building a gourd banjolele -- a whole lot of fun watching the instrument take shape over the course of the week.
posted afternoon of June 17th, 2018: 1 response ➳ More posts about the Family Album
|  |
Sunday, July 8th, 2012
One day,  -- the next,  Time to rent a chainsaw... I seem to remember hearing dogwood makes nice carving/turning wood, will try to get some blanks out of this.
posted morning of July 8th, 2012: Respond ➳ More posts about The garden
|  |
Saturday, January 8th, 2011
David Bonta (blogger at Via Negativa) has published a book of Odes to Tools with Phœnecia Publishing -- some beautiful thoughts about the things we use.
Ode to a Socket WrenchBetter than all power tools Is the socket wrench:
Its accomodating nature Its chrome-plated steel Its handling of torque. Kristin Berkey-Abbott reviews the collection today.
posted morning of January 8th, 2011: Respond ➳ More posts about Readings
|  |
Saturday, March 15th, 2008
For a while my A string has been fraying and in need of replacement -- tonight I put a new string on. Well a couple of things about this: it took a frustratingly long time to get it on and wound properly, a job that should take less than a minute. So I'm frustrated about not being skillful at it. But more, I don't like how long it took me to get around to doing it -- I get intimidated by stuff like this in a really not useful way. Both of these things are also true of sharpening knives, and it drives me crazy that all the knives in my kitchen and most of the blades in my wood shop are not sharp the way they ought to be, and how intimidated I get at the thought of making them sharp. I'm not sure how to approach this.
posted evening of March 15th, 2008: Respond ➳ More posts about Fiddling
|  |
Thursday, January 10th, 2008
I have 3 woodworking projects that I would like to get done this winter (and that Ellen would like me to get done this winter): - A decoration for the front of the walk in front of our house, in the form of a short fence or two short fences with a post at the corner. Ideally with nice carved finials at the top of the fence stakes. We want to grow some kind of vine or rosebush against this.
- A bench for the front entry. Size is kind of tricky since the entry is mostly occupied by the swing of the front door; but there is a corner where a narrow bench would fit. Ideally this will be of the same wood and vaguely similar design to my garden bench in the front yard.
- If I get ambitious, a similar bench for the top of the staircase.
I haven't been in my wood shop much at all in the past few years; but I have been wanting to do more with my hands. So I better seize the day.
posted afternoon of January 10th, 2008: Respond
| Previous posts about Woodworking Archives  | |
|
Drop me a line! or, sign my Guestbook. • Check out Ellen's writing at Patch.com.
| |